Geocaching on Mars: How Perseverance Will Seal Martian Samples with a Return to Earth in Mind
With the roughly 20-day wide launch window for the Mars 2020 mission rapidly approaching, the hype train for the next big mission to the Red Planet is really building up steam. And with good reason — the Mars 2020 mission has been in the works for a better part of a decade, and as we reported earlier this year, the rover it’s delivering to the Martian surface, since dubbed Perseverance, will be among the most complex such devices ever fielded.
“Percy” — come on, that nickname’s a natural — is a mobile laboratory, capable of exploring the Martian surface in search of evidence that life ever found a way there, and to do the groundwork needed if we’re ever to go there ourselves. The nuclear-powered rover bristles with scientific instruments, and assuming it survives the “Seven Minutes of Terror” as well as its fraternal twin Curiosity did in 2012, we should start seeing some amazing results come back.
No prior mission to Mars has been better equipped to answer the essential question: “Are we alone?” But no matter how capable Perseverance is, there’s a limit to how much science can be packed into something that costs millions of dollars a kilogram to get to Mars. And so NASA decided to equip Perseverance with the ability to not only collect geological samples, but to package them up and deposit them on the surface of the planet to await a future mission that will pick them up for a return trip to Earth for further study. It’s bold and forward-thinking, and it’s unlike anything that’s ever been tried before. In a lot of ways, Perseverance’s sample handling system is the rover’s raison d’être, and it’s the subject of this deep dive.
Three Robots in One
NASA has done its usual admirable job of communicating with the public about the Mars 2020 mission, and part of the outreach includes this recent video that shows off a little of the engineering that went into the sample handling system. Honestly, though, for as much tech eye candy as that video had, it only served to whet my appetite. There was so much going on that I had to find out more.
To get a bit of the inside story, I turned to Kelly Palm, one of the JPL engineers seen in the video below. As the Integration and Test Lead for the Sample Caching System (SCS), she’s pretty busy these days, but she graciously fielded my questions and helped give me an idea of what went into building and testing such a complex piece of equipment.
First of all, the SCS is really not just one but three separate robots, each with a specific set of jobs. The “business end” of the SCS is the 2-meter-long robot arm mounted to the front of the vehicle. Like Curiosity before it, the arm carries a turret that’s laden with scientific instruments, sensors, and cameras, as well as the tools necessary for boring into Martian rocks and taking samples. But unlike its predecessor, where the rock drill was designed to abrade rocks and produce a powder that could be easily analyzed by onboard instruments, the Perseverance drill is specialized for obtaining core samples, suitable for both on-board study and in terrestrial labs once the samples are returned.
The drill in the robot arm’s turret is a pretty versatile tool. With the help of the bit carousel (more about which is below) the drill can attach bits designed for different jobs. The drill is capable of running in either a simple rotary mode or in a percussive mode, similar to a hammer drill. A small onboard tank of purified nitrogen is used to gently remove dust generated by coring operations.
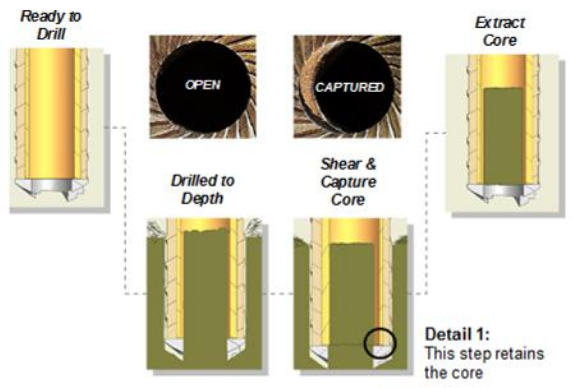
Coring into rock to a limited depth using a cylindrical bit raises a question: how exactly is the core recovered? On Earth, the answer would be to use a second tool to pry at the cylinder of rock left behind after the coring bit is removed. While something like that could certainly work on Mars too, especially with a robotic arm at your disposal, NASA came up with a far more clever system.
According to design tests run by a company called Honeybee Robotics in 2014, liberating the core from the parent rock and enclosing it the sample tube in which it will live until being reopened in a lab on Earth is a one-step process. Nestled inside the coring bit is a titanium sample tube. During coring, the axis of the sample tube and the coring bit are aligned with each other, so that the tube slips over the rock core as drilling proceeds. At the proper depth, the sample tube is rotated slightly off-axis, exerting enough force on the base of the core sample to break it off from the parent rock. The core is retained by a lip on the inside of the coring bit, allowing it to be removed from the hole, already within the titanium sample tube in which it will remain until the sample return mission.
Sealed with a Ram
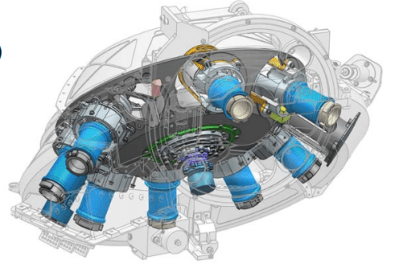
The bit carousel is the next robot in the sample caching process. Sitting at the front of the rover chassis, the bit carousel is outwardly simple — just a rotating turret that transports bits to and from storage in the belly of Perseverance. But what it lacks in complexity is more than made up for by its clever design. The body of the carousel is a wheel with stations around the edge. Each station is at a 45° angle relative to the rotor’s axis, which itself is oriented 45° to the long axis of the chassis. The combination of angles means that a tube can transition from vertical to horizontal just by rotating the carousel with a single motor. There are plenty of sensors and actuators that ensure everything is lined up, of course, but the simplicity of the design is really something.
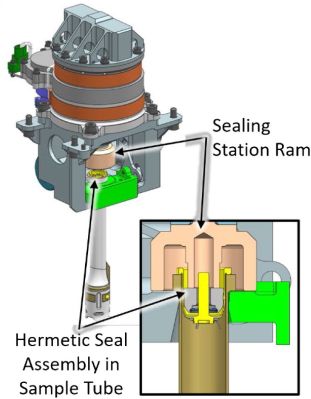
The ability to transfer tools and samples between horizontal and vertical orientations is critical to the sample caching mission, since the robot that takes care of storing everything lives inside the forward section of the rover’s chassis. The Sample Handling Arm, or SHA, looks a little like the SCARA (selective compliance articulated robot arm) robots that are prevalent in semiconductor fabs. The SHA is capable of accessing multiple locations inside the sample caching compartment and transferring between them and the bit carousel presentation area. To clear the instruments and sample tubes that take up most of the space in the bay, the SHA has an additional Z-axis so that the whole thing can drop below the bottom edge of the rover chassis. In addition to 42 storage silos for core and regolith sample tubes, the SHA can reach storage for a number of tools and attachments, plus instruments for doing some preliminary analysis of the samples, such as volume assessment and imaging.
Once a sample tube is filled, it needs to be hermetically sealed to ensure that the contents will survive for an indeterminate amount of time on the Martian surface as well as withstand the rigors of the eventual trip back to Earth. The seal has to be made without contaminating the sample, so no adhesives can be used, and no heat can be used either, lest the sample be subjected to extreme temperatures.
To seal a sample tube, the SHA brings it over to one of seven seal dispensers. A cup-shaped plug is dropped into the open end of the tube by a dispenser. The plugged tube is then moved to a sealing station, which uses a motor-driven ram to drive a tapered ferrule down a guide rod inside of the plug. As the ferrule is pressed downward, the rim of the plug expands, driving a sharp tooth on its outside circumference into the inner wall of the sample tube. The end result is essentially a cold-welded bond between the cap and the sample tube, hermetically sealing the tube and protecting the sample from contamination.
Return to Sender
Once a sample has been sealed in its titanium sarcophagus, it’s ready to be deposited onto the Martian surface. Most mission profiles that I could find refer to the use of “depot caching”, where Perseverance repeatedly returns to a single location from various regions of interest to deposit sample tubes. This makes perfect sense; finding a big pile of 42 titanium tubes is probably a far easier task for a future sample recovery mission than roaming about looking for individual tubes dropped where they were taken.
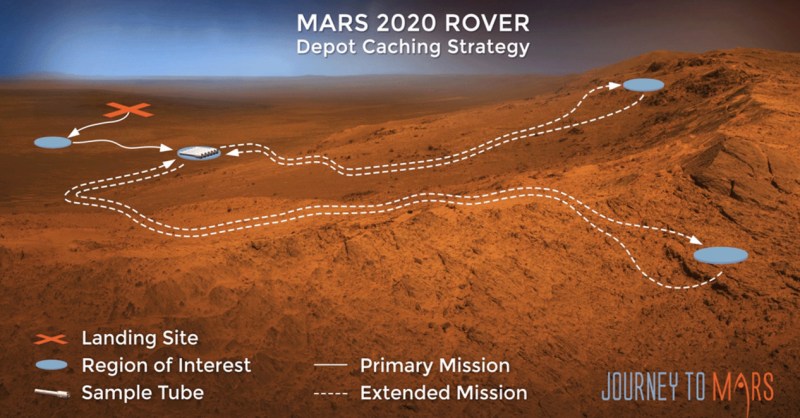
Still, whatever robot is sent to clean up after Perseverance has its work cut out for it; since the SHA cannot reach down to the surface, the tubes will have to be dropped, which means an orderly stack of sample tubes will likely not be what the recovery robot will find. Whatever follows in Perseverance’s tracks is going to need the agility to pick up and safely stow every single precious sample tube regardless of its orientation, possibly after digging it out of wind-blown regolith, and the intelligence to do it all autonomously.
With some luck, Perseverance will soon be on its way to Mars, and both when it launches and when it lands in February, we’ll be glued to our seats waiting for results. We’ll also be following the development of the return mission, which could prove to be even more challenging and require even cooler engineering to pull off.
Featured images: NASA/JPL-Caltech
from Blog – Hackaday https://ift.tt/2EwkMoR
Comments
Post a Comment